Flooring might not be the flashiest part of a home or business renovation, but it’s absolutely one of the most critical. When you walk into a room, the floor is literally the foundation beneath your feet—affecting everything from comfort and acoustics to how the space looks and feels. Over the past few years, SPC (Stone Plastic Composite) flooring has skyrocketed in popularity because it’s durable, water-resistant, and surprisingly stylish. But did you know there’s a whole world of different SPC types out there?
SPC flooring is a rigid vinyl plank that combines limestone, PVC, and stabilizers for exceptional durability. Its dense core resists dents and moisture better than traditional vinyl or laminate. Different types vary in core composition, wear layer thickness, and finishes, allowing homeowners and businesses to choose the perfect balance of toughness, design, and comfort.
Maybe you’re renovating a cozy living room, turning your basement into a home theater, or outfitting a bustling restaurant. Whatever your project, understanding SPC’s diverse options can save you from unnecessary headaches—like floors that warp under humidity or scuff easily under heavy foot traffic. In this guide, we’ll go deep into the many types of SPC flooring, using a friendly, conversational style. Plus, you’ll find real-life tips, data, and easy-to-copy tables to help you decide which SPC floor is “the one.” Stick around—you might just find the perfect match for your space.
1. What Exactly Is SPC Flooring, and Why Is It Unique?
SPC is a vinyl floor with a rigid stone-plastic composite core. Its stone content boosts stability and dent resistance, making it stand out from standard vinyl or laminate, especially in areas prone to water or high foot traffic.
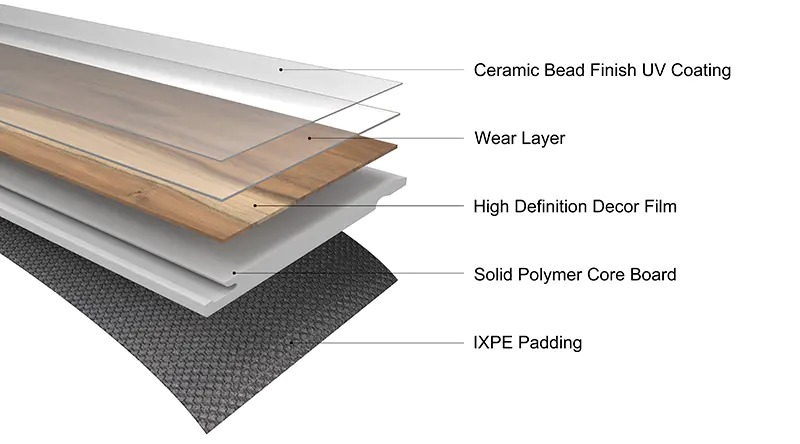
Core Reasons SPC Flooring Shines
You might wonder: “Why bother with SPC when traditional vinyl and laminate are so common?” Let’s unpack the unique qualities that have everyone buzzing about SPC.
1.1 The Stone-Plastic Core
- Limestone Meets PVC: Think of SPC’s core as a blend of finely ground limestone (calcium carbonate) mixed with PVC and some stabilizers. This mix creates a floor that’s rigid—so it won’t easily bend or dent.
- Not Your Grandma’s Vinyl: Traditional vinyl floors can flex or even ripple under heat. SPC’s denser composition helps it stay put, even in rooms with big windows where sunbeams can cause temperature swings.
1.2 Water Resistance and Stability
- Totally Waterproof: SPC floors shrug off spills or high humidity like it’s no big deal. Perfect for kitchens, bathrooms, or damp basements.
- No More Warping Woes: Because of its stable core, SPC handles shifting temperatures and moisture far better than wood-based floors. If you’ve had nightmares of warped planks, SPC might be your hero.
1.3 Comfort and Noise Control
- Underlayment Extras: Many SPC floors come with attached underlayment (like EVA or IXPE foam), adding a cushiony feel and reducing noise.
- Goodbye Hollow Sounds: You know that “click-click” noise some laminate floors make? SPC typically gives you a more solid, grounded sound—something you’ll appreciate in open-concept homes or multi-story buildings.
Feature | Why It Makes SPC Flooring Unique |
---|---|
Stone-Plastic Core | Made from limestone (calcium carbonate) + PVC, resulting in a rigid, dent-resistant core. |
Heat Stability | Unlike traditional vinyl, SPC resists rippling or warping from sunlight or heat exposure. |
Waterproof Performance | Completely waterproof—ideal for bathrooms, kitchens, and basements. |
Dimensional Stability | Handles temperature and humidity changes without swelling or warping. |
Attached Underlayment | Many SPC products include EVA or IXPE foam layers for added comfort and sound absorption. |
Noise Reduction | Feels and sounds more solid than laminate—no hollow “clicking” noise. |
Overall Benefit | Combines the water resistance of vinyl with the strength of laminate or tile, plus added comfort. |
All in all, SPC’s blend of toughness and comfort is a huge selling point. It’s like combining the best of vinyl (easy maintenance, water resistance) with the sturdiness you might associate with laminate or even tile.
2. Which Core Constructions Distinguish Different SPC Flooring Types?
SPC floors differ in core density, stone-to-PVC ratios, and stabilizer quality. These variations affect rigidity, impact resistance, and how the floor handles temperature or moisture swings.
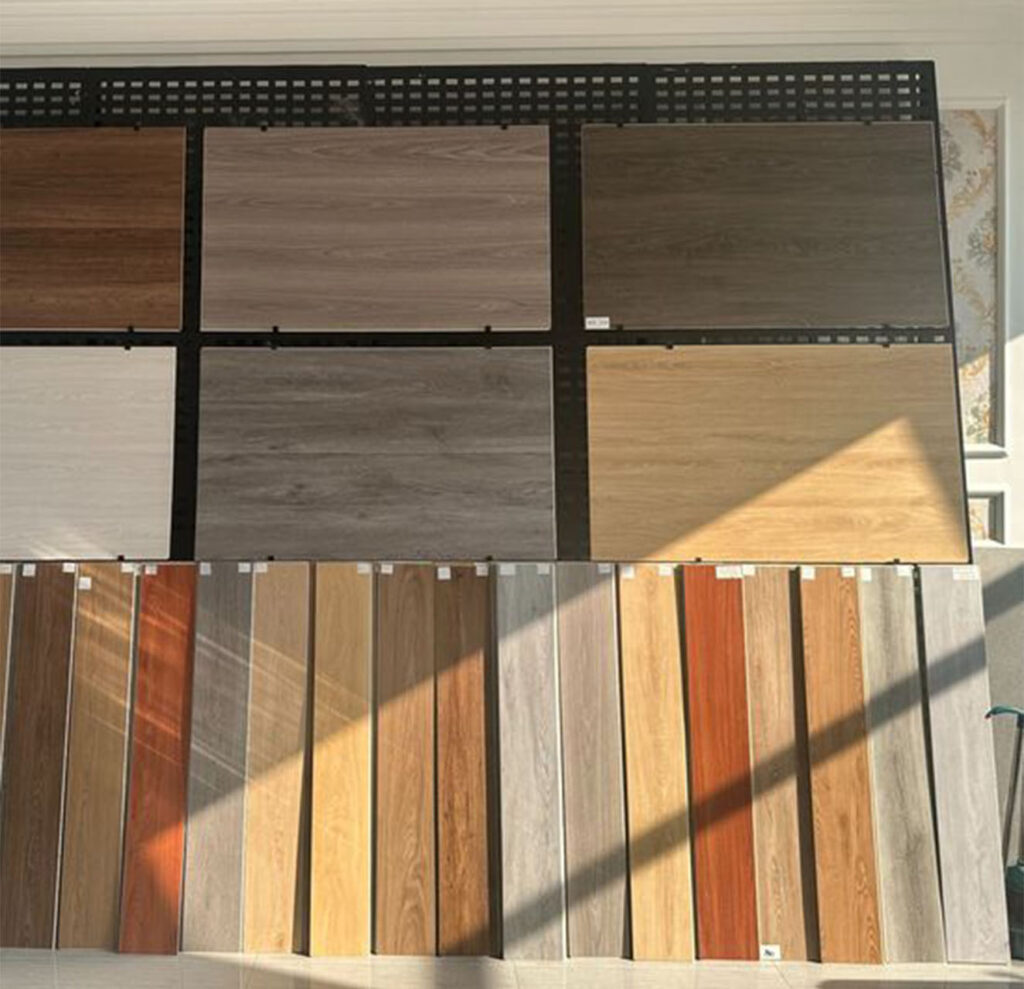
Unpacking the Core’s Role
Though SPC floors share a similar stone-plastic formula, the exact blend can vary widely, giving each type unique benefits.
2.1 Single-Layer vs. Multi-Layer Cores
- Single-Layer Cores
- Straightforward Composition: A uniform blend of stone dust and PVC.
- Budget-Friendly: Fewer production steps can translate to a lower price.
- Possible Downsides: Might not absorb as much impact or sound as multi-layer alternatives.
- Multi-Layer Cores
- Extra Reinforcement: Some SPC floors stack multiple layers of stone-plastic composite to enhance stability and resilience.
- Better for Busy Spaces: Multi-layer cores often handle furniture movements or foot traffic more gracefully.
2.2 Stone-to-PVC Ratios
- High Stone Content:
- A core with lots of limestone is ultra-rigid and resists denting like a champ.
- Could be heavier, which might affect shipping costs or the ease of installation.
- Balanced Blend:
- More PVC in the mix means a touch more “give” underfoot.
- Still plenty tough, just slightly less dense than high-stone options.
2.3 Stabilizers and Quality Control
- Thermal Stability: Stabilizers help the plank cope with dramatic temperature swings—think hot summer days or cold winter nights.
- Brand Reliability: Reputable SPC brands often use top-notch stabilizers, leading to fewer issues like warping or “cupping” (edges curling up).
Here’s a handy table comparing how different core factors affect performance:
Core Factor | Description | Ideal Scenario |
---|---|---|
Stone-to-PVC Ratio | Dictates rigidity and weight | High traffic or heavy loads (commercial, busy homes) |
Single vs. Multi-Layer | Impacts sound absorption, stability, and comfort | Multi-layer for bigger spaces or to minimize floor noise |
Stabilizer Quality | Improves temperature and dimensional stability | Regions with extreme climate shifts or direct sunlight |
Picking a core construction that fits your lifestyle can mean the difference between a floor that holds up beautifully for years versus one that struggles under your day-to-day realities.
3. How Do Wear Layer Thicknesses and Treatments Affect Performance?
A thicker wear layer, plus specialized treatments like UV or anti-scratch coatings, can significantly increase durability, reducing visible scuffs, fading, and general wear.

Safeguarding Your Flooring Investment
Think of the wear layer like a suit of armor for your flooring. The thicker and more advanced it is, the better your floor can handle daily abuse.
3.1 Decoding Wear Layer Measurements
- Mil vs. Millimeter: “Mil” is 1/1000 of an inch. So, a 12 mil wear layer equals about 0.30 mm thick. Don’t confuse “mil” with “mm” (millimeters).
- Common Ranges:
- 6–8 mil: Good for low-traffic rooms or budget-friendly installs.
- 12–20 mil: The sweet spot for most homes, handling kids, pets, and moderate foot traffic.
- 20+ mil: Ideal for commercial or truly high-traffic residential spaces.
3.2 Protective Coatings and Extras
- UV Curing
- Shields the floor from discoloration due to sunlight.
- Handy if you have big windows or plan to install the floor in a sunroom.
- Anti-Scratch Treatments
- Perfect for pet owners or busy households.
- Minimizes those pesky surface scratches from moving chairs, rolling toys, or excited dogs.
- Anti-Microbial Layers
- Some high-end SPC floors claim to fight bacteria or mold growth, a plus for hospitals, daycare centers, or allergen-sensitive homes.
3.3 Matching Wear Layers to Your Space
- Quiet Guest Rooms: 6–8 mil might suffice, as the room won’t see heavy traffic.
- Kitchen or Family Room: Aim for 12+ mil to handle daily hustle and bustle.
- Commercial or Retail: 20 mil and above, ensuring minimal scuffing from customers and carts.
Aspect | Key Insights & Recommendations |
---|---|
Mil vs. Millimeter | 1 mil = 1/1000 inch ≈ 0.0254 mm. Don’t confuse mil (imperial) with mm (metric). |
Wear Layer Thickness Guide | 6–8 mil: Light residential use (e.g., guest rooms). 12–20 mil: Ideal for most homes. 20+ mil: Best for commercial or high-traffic areas. |
UV Coating | Prevents sun fading—great for sunrooms or rooms with large windows. |
Anti-Scratch Treatment | Protects against surface scratches—especially useful for pet owners or active households. |
Anti-Microbial Layer | Helps resist bacteria and mold—ideal for healthcare settings or allergy-prone homes. |
Room-by-Room Recommendation | Guest Rooms: 6–8 mil Living Rooms/Kitchens: 12+ mil Commercial Spaces: 20+ mil |
Long-Term Value | Thicker wear layers reduce long-term maintenance and replacement costs. |
Investing in a thicker wear layer might cost a bit more upfront, but it often pays off in fewer repairs or plank replacements down the line.
4. Are There Various Surface Finishes and Designs for SPC Flooring?
Absolutely. SPC offers smooth, lightly embossed, or deep-embossed surfaces, plus a huge range of wood, stone, and even patterned designs to suit any interior style.
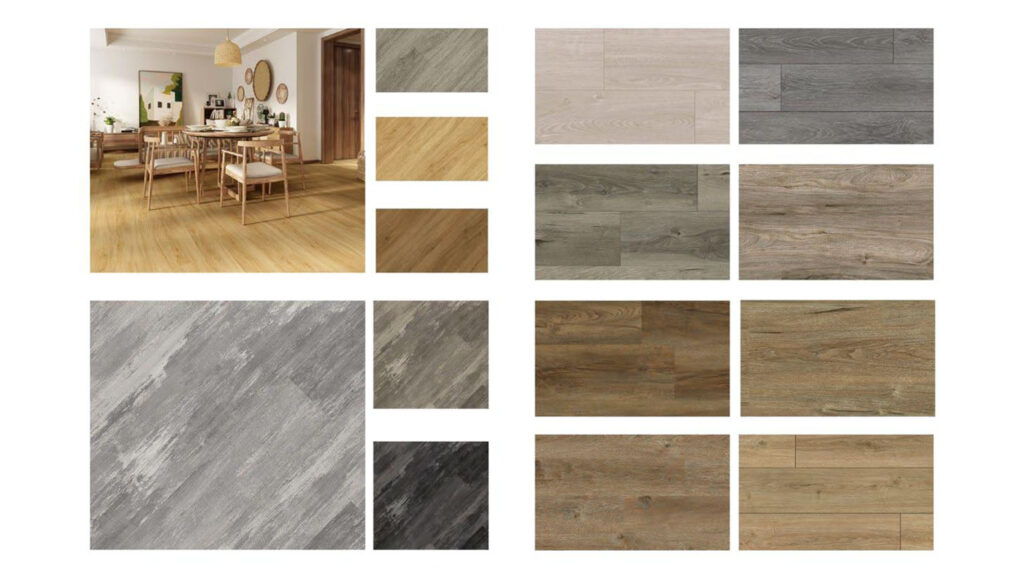
Expressing Personal Style with SPC
Gone are the days when vinyl floors only came in bland colors or patterns. Modern SPC flooring can closely mimic high-end hardwood, ceramic tiles, or natural stone—often at a fraction of the cost.
4.1 Textures: Embossing vs. Smooth
- Embossed-in-Register (EIR)
- Lines up the embossed texture with the printed wood grain for ultra-realistic “knots” and “grain.”
- Gives you the look and feel of actual hardwood, which can fool even the most discerning visitors.
- Light Embossing
- Adds gentle depth without a dramatic texture.
- Balances traction and easy cleaning—perfect for busy families or seniors who want slip-resistance.
- Smooth Surfaces
- Easiest to wipe down but can be more slippery when wet.
- Ideal in modern, minimalist designs that favor clean lines.
4.2 Design Themes
- Wood-Look SPC:
- Emulates everything from rustic oak to chic gray-washed pine.
- Great if you love the warmth of wood but want water resistance.
- Stone or Tile Look:
- Mimic marble, slate, or even travertine without the upkeep and coldness underfoot.
- Popular in contemporary kitchens or spa-inspired bathrooms.
- Patterned Styles:
- Herringbone, chevron, or creative geometric motifs are trending.
- Installation is more involved, but the visual payoff can be stunning.
4.3 Coordinating with Your Décor
- Farmhouse Aesthetic:
- Choose deeper embossing with distressed or weathered wood looks.
- Pair with warm rugs and rustic furniture for a cozy vibe.
- Urban Chic:
- Smooth or lightly embossed finishes with bold stone or concrete visuals.
- Complement with exposed brick walls, metal fixtures, and open floor plans.
- Classic Luxury:
- Consider high-gloss finishes that mimic polished marble or exotic hardwood.
- Perfect for formal dining rooms or upscale retail boutiques.
Category | Options & Highlights | Best For/Style Match |
---|---|---|
Surface Texture | Embossed-in-Register (EIR): Matches texture to printed grain for ultra-realistic wood feel. Light Embossing: Subtle texture, good balance of grip and cleanability. Smooth: Sleek look, easy to clean, can be slippery. | EIR: Authentic wood-look lovers Light Embossing: Families, seniors Smooth: Modern, minimalist spaces |
Design Themes | Wood-Look: Oak, pine, walnut, gray-washed styles. Stone/Tile Look: Marble, slate, travertine. Patterned: Herringbone, chevron, geometric layouts. | Wood-Look: Cozy, warm interiors Stone/Tile: Kitchens, bathrooms Patterned: Bold, custom spaces |
Décor Pairing Suggestions | Farmhouse: Distressed wood textures, warm tones, rustic accents. Urban Chic: Concrete or stone visuals, smooth finishes, industrial touches. Classic Luxury: High-gloss marble or exotic hardwood look. | Farmhouse: Rugs, natural wood décor Urban Chic: Metal, brick, open spaces Classic Luxury: Formal, upscale rooms |
Picking the right finish and design can truly elevate your space—so don’t be afraid to get creative. SPC is all about blending fashion with function.
5. Do Installation Methods Differ Across Various SPC Flooring Types?
Yes. While click-lock is most common and user-friendly, some SPC lines require glue-down for maximum stability, especially in high-traffic or commercial areas.
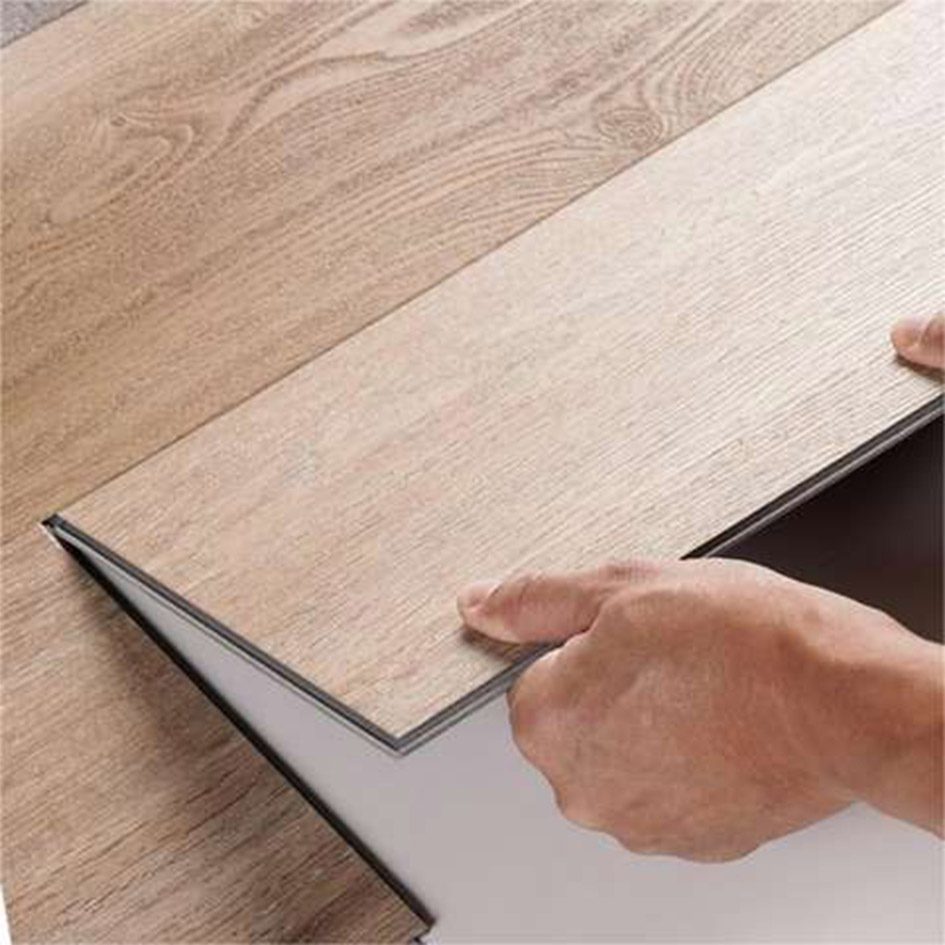
Figuring Out the Best Installation Method
Your choice between click-lock or glue-down can have a big impact on cost, installation time, and long-term maintenance.
5.1 The Click-Lock (Floating) Approach
- Easier DIY Project
- Planks snap or “click” together along edges, resting on the subfloor without direct adhesion.
- Quick to install, often with minimal tools—handy for weekend warriors.
- Subfloor Must Be Level
- Floating floors can highlight lumps or dips in the subfloor.
- Consider a leveling compound or subfloor prep if you want a seamless finish.
- Expansion Gaps
- Because the floor “floats,” you’ll typically leave a small gap around walls to accommodate natural expansion.
- Baseboards or quarter-round trim hide these gaps nicely.
5.2 Glue-Down SPC
- Stronger Bond
- A layer of adhesive attaches each plank to the subfloor.
- Great in commercial settings or places with heavy furniture, like pianos or pool tables.
- Precision Matters
- Adhesive must be spread evenly and consistently.
- Mistakes can be messy or cause planks to pop up over time.
- Repair Challenges
- Replacing damaged planks can be trickier since they’re firmly stuck down.
- Hiring a professional installer might be worth the cost for larger or complex layouts.
5.3 Hybrid Methods
- Click-Lock + Perimeter Glue
- Sometimes done in high-moisture areas for extra peace of mind.
- Easy installation with added stability around edges.
- Peel-and-Stick Edges
- Less common but still out there. The planks lock together and use adhesive strips at the seam for extra hold.
Installation Method | Key Features & Considerations | Best Use Cases |
---|---|---|
Click-Lock (Floating) | – Planks snap together without adhesive – DIY-friendly, quick installation – Requires a level subfloor – Leave expansion gaps around perimeter | – Residential spaces – DIY projects – Shorter timelines |
Glue-Down SPC | – Adhesive secures planks directly to subfloor – Stronger bond for heavy furniture or rolling loads – Requires even adhesive application – Harder to repair | – Commercial/high-traffic areas – Rooms with heavy furniture |
Hybrid: Click-Lock + Perimeter Glue | – Combines floating ease with added edge stability – Used in areas prone to moisture | – Bathrooms, kitchens, laundry rooms |
Peel-and-Stick Edges | – Less common – Adhesive strips add seam grip – Limited to select product lines | – Small DIY spaces or temporary installs |
Before you commit, think about your skill level, timeline, and how much foot traffic the space will see. Floating floors are simpler to install; glue-down offers top-notch stability.
6. When Is Waterproof or Rigid-Core SPC the Best Choice?
Pick rigid-core, waterproof SPC for moisture-heavy zones—bathrooms, kitchens, basements—or high-traffic commercial spaces needing maximum stability and dent resistance.
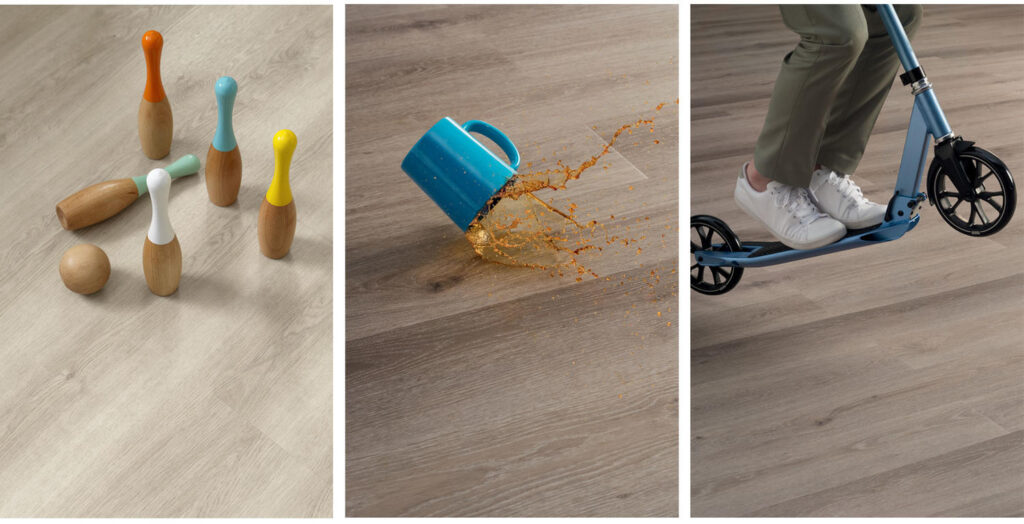
Why “Waterproof” and “Rigid-Core” Matter
All SPC floors are water-resistant, but some take it to another level. If you see “rigid-core waterproof” on the label, that’s a sign the floor can handle more extreme conditions.
6.1 Perfect for Damp or Varied Environments
- Kitchens, Bathrooms, Laundry Rooms:
- Frequent spills or splashes? Rigid-core SPC stays intact without warping.
- Mopping or minor flooding events (like a leaky dishwasher) are less stressful.
- Basement Installations:
- Basements often battle humidity or ground moisture.
- Rigid-core SPC is less likely to develop mold or bubble at the edges if small leaks occur.
6.2 Consistent Performance Under Stress
- High Traffic, Big Equipment:
- Commercial kitchens, retail stores, or busy offices see constant foot traffic.
- Rigid-core SPC handles rolling carts or chair wheels better than softer floors.
- Temperature Extremes:
- Some floors expand or contract wildly in sunrooms or near large windows.
- Rigid-core designs help prevent buckling or seam separation.
6.3 Cost vs. Benefit
- Higher Upfront Investment:
- Premium SPC lines often carry a heftier price tag.
- Long-Term Savings:
- Fewer repairs or plank replacements.
- Less downtime if a mishap occurs (e.g., no need to rip up waterlogged boards).
Scenario / Feature | Why Rigid-Core Waterproof SPC Is Ideal |
---|---|
Moisture-Prone Areas | Perfect for kitchens, bathrooms, and laundry rooms—resists warping from spills or mopping. |
Basement Installations | Handles ground moisture and humidity well; resists mold, bubbling, and edge damage. |
High Traffic or Heavy Equipment | Withstands rolling carts, chairs, and constant foot traffic—great for offices or retail. |
Temperature Extremes | Maintains dimensional stability near windows or in sunrooms—less risk of buckling or seam gaps. |
Cost vs. Long-Term Value | Higher initial cost, but fewer repairs and longer lifespan reduce overall flooring expenses. |
Best Use Cases | Bathrooms, kitchens, basements, commercial spaces, sunrooms, and anywhere with high wear or moisture. |
If your space is prone to any sort of moisture, from daily splashes to occasional leaks—or if you just want rock-solid flooring with minimal chance of denting—opt for a robust, rigid-core SPC.
7. What Factors Should You Consider When Choosing Among SPC Flooring Types?
Balance your budget, subfloor conditions, foot traffic, and style preferences. Think about wear layer needs, installation method, and climate to pinpoint the ideal SPC floor.
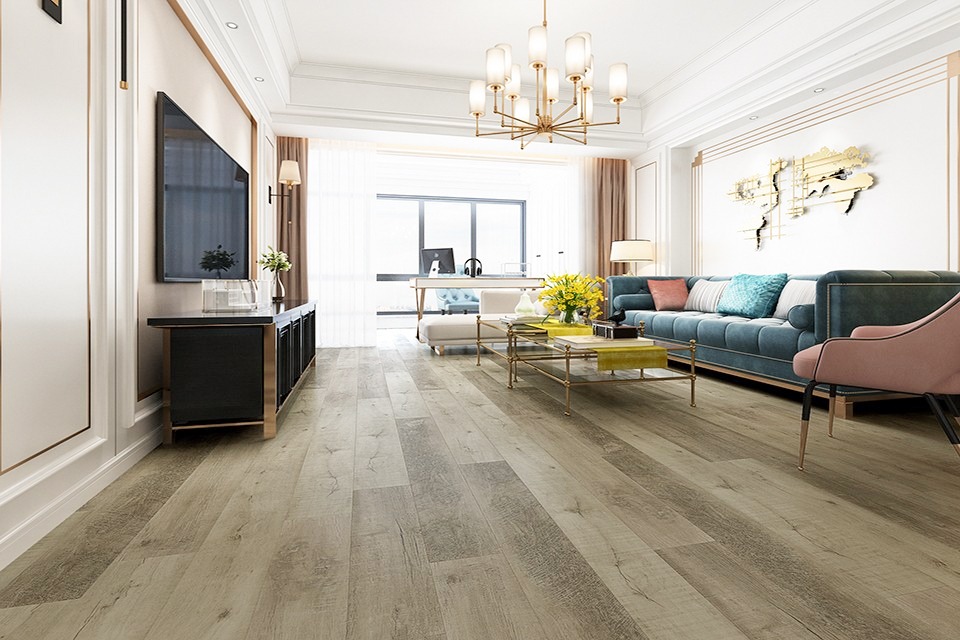
Making the Right Match for Your Space
Picking an SPC floor isn’t just about color samples and price tags. It’s about syncing up real-life needs with the floor’s strengths.
7.1 Budget vs. Performance
- Wear Layer Thickness
- If you have rambunctious kids or pets, aim for at least 12–20 mil.
- Lower-traffic spaces might get by with 8 mil or so, saving some cash.
- Brand and Stabilizer Quality
- Cheaper SPC might be tempting, but corners can be cut in stabilizer selection or core uniformity.
- Investing a bit more in a reputable manufacturer often pays off in fewer headaches down the line.
7.2 Subfloor Condition and Climate
- Flatness Requirements
- Floating floors especially need a fairly level subfloor. Check for dips or ridges over 3–4 mm.
- Glue-down can sometimes handle slight imperfections but still requires a decent base.
- Humidity and Temperature
- If you live in a region with big seasonal swings, consider rigid-core or multi-layer options.
- Basements, in particular, might benefit from moisture barriers or thicker core planks.
7.3 Usage and Lifestyle
- Foot Traffic
- Busy households with kids or multiple pets can wear floors down quickly.
- Commercial settings might need that 20+ mil wear layer to stay pristine.
- Style Preferences
- Are you aiming for cozy, rustic vibes or a sleek, modern look?
- Heavier embossing suits a farmhouse aesthetic; smooth or stone visuals complement contemporary spaces.
7.4 Maintenance and Repairs
- Cleaning Routine
- SPC floors are low maintenance, but check if special cleaners are required for certain finishes or anti-microbial layers.
- Avoid harsh chemicals that could degrade the wear layer over time.
- Replacement Ease
- Click-lock floors let you swap out a damaged plank (if you have spares) without redoing the entire floor.
- Glue-down floors or patterned layouts can make spot repairs trickier.
Consideration Category | Key Factors to Evaluate | Recommendations / Tips |
---|---|---|
Budget vs. Performance | – Wear layer thickness (8 mil for light use, 12–20+ mil for active homes or commercial spaces) – Brand and stabilizer quality affect longevity | Choose trusted brands and appropriate wear layer for your lifestyle |
Subfloor & Climate | – Floating floors need a level subfloor (no dips > 3–4 mm) – Glue-down tolerates slight imperfections – Climate extremes require stable, rigid cores | Use leveling compound if needed; consider moisture barriers in basements |
Foot Traffic & Usage | – Kids, pets, or heavy commercial use demand higher durability – Match texture to lifestyle and design preferences | 20+ mil wear layer for busy areas; embossed textures for rustic spaces |
Style Preferences | – Rustic/farmhouse: choose deep embossing, wood-look – Modern: opt for smooth finishes or stone visuals | Coordinate with furniture and overall décor theme |
Maintenance & Repairs | – Easy to clean with pH-neutral products – Click-lock allows easier plank replacement – Glue-down or patterns may complicate repairs | Keep spare planks on hand; avoid harsh cleaners |
When choosing your SPC floor, imagine living with it day in and day out. Will it hold up to muddy shoes, spilt drinks, or the occasional rolling office chair? Matching these practical considerations with a design you love ensures you’ll be thrilled with your choice long after installation day.
Conclusion: Ready to Find Your Ideal SPC Flooring? Contact Kinwin
SPC flooring isn’t just another vinyl product. Thanks to its dense, stone-plastic core, impressive wear layers, and diverse finishes, SPC can adapt to just about any setting—from splash-prone bathrooms to chic downtown offices. The key is knowing the differences: which cores are heavier or lighter, how wear layers and special coatings impact durability, and why installation method matters more than you might guess.
Feeling a bit overwhelmed by all the details? That’s perfectly normal. Flooring is a big investment—one that, if chosen wisely, will keep you smiling (and your feet comfy) for years. At Kinwin, we get it. We specialize in crafting high-quality SPC solutions that balance style, durability, and affordability. Whether you’re leaning toward a multi-layer rigid-core for a lively restaurant or a softer underlayment for a quiet nursery, our team is ready to help you navigate the options.
Reach out to Kinwin today for a custom quote or more detailed product info. Let’s partner up to create the perfect floor for your unique space—one that stands up to life’s little surprises and looks fantastic doing it.