Flooring is a big deal—it sets the tone and feel of any space, whether you’re renovating a cozy living room or reimagining a bustling commercial storefront. With vinyl flooring long established as a versatile, budget-friendly hero, there’s now a rising star in the market: SPC flooring. You might’ve seen it mentioned in online reviews or heard a contractor rave about its durability. So what’s the real story?
SPC (Stone Plastic Composite) flooring is an advanced version of vinyl flooring that features a rigid, limestone-based core for improved stability, dent resistance, and minimal expansion. Traditional vinyl is more flexible and budget-friendly but generally less robust under heavy use or temperature swings. SPC excels in demanding conditions, while vinyl suits lighter traffic and simpler needs.
The key is knowing how they differ—and how these differences might make a real impact on your daily life. Imagine installing a floor you think is tough enough, only to find it scuffs easily or warps after a hot summer. That’s a headache nobody wants! In this guide, we’ll break down the details, explore which flooring stands up best to moisture and foot traffic, discuss costs, share data you can use, and offer a few personal anecdotes. Stick around for stories, facts, and examples that just might save you from a flooring fiasco.
1. What Exactly Is SPC Flooring, and How Does It Differ From Standard Vinyl?
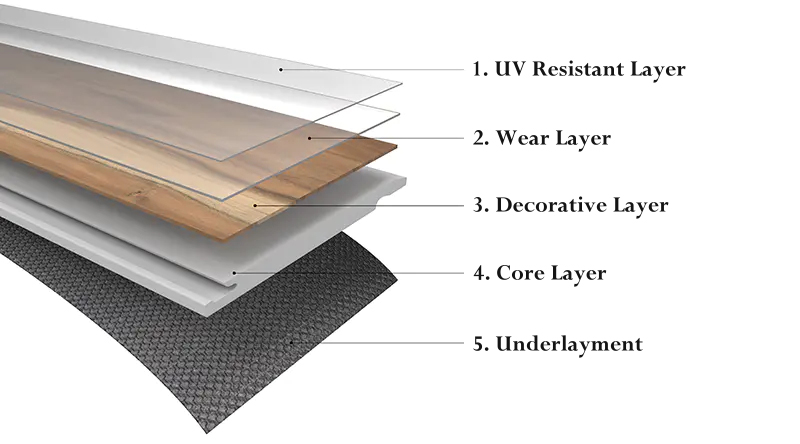
SPC flooring has a stone-based, rigid core for extra stability and dent resistance, while standard vinyl flooring relies on a more flexible plastic core. SPC often handles stress and climate shifts better than typical vinyl.
The Basics of SPC and Vinyl
Let’s start with a solid foundation. If you’ve ever come across terms like “LVT” (luxury vinyl tile) or “LVP” (luxury vinyl plank), you’re on the right track—SPC is part of the broader vinyl family, just with a unique twist.
1.1 Understanding SPC Flooring
- Stone Plastic Composite Core: The “SP” in SPC stands for stone plastic—often limestone (calcium carbonate) mixed with PVC powder. This robust core doesn’t flex as much as typical vinyl, which is why SPC planks feel firmer underfoot.
- Why Does It Matter? The rigid core helps prevent dents and dings. So, if you drop a pot or if your sofa has ultra-thin legs, SPC flooring is less likely to show those little circular indentations you sometimes see on softer floors.
1.2 Standard Vinyl in a Nutshell
- More Flexibility: Traditional vinyl uses multiple layers of PVC. It’s durable but has a bit more “give.” For example, if your subfloor isn’t perfectly even, standard vinyl might follow the subfloor’s contours more closely.
- Budget-Friendly Variety: Vinyl flooring is often the go-to for homeowners on a budget, with a broad range of price points. You can find everything from thin, peel-and-stick sheets to thicker luxury vinyl planks that rival SPC in looks.
1.3 Real-Life Example: A Busy Kitchen
- SPC Scenario: In a home with four kids racing around or in a commercial cafe, an SPC floor might resist foot traffic and accidental impacts (like dropped pans) better. It’s also less likely to warp from steam around the stove.
- Vinyl Scenario: For a quieter household with moderate cooking and less daily foot traffic, a quality vinyl plank could still provide excellent performance—usually at a lower cost.
Feature | SPC Flooring (Stone Plastic Composite) | Standard Vinyl Flooring |
---|---|---|
Core Composition | Rigid core made of limestone (calcium carbonate) and PVC. | Flexible core made of multiple layers of PVC. |
Durability & Dent Resistance | Highly resistant to dents and dings, making it ideal for high-traffic areas. | More flexible but can show indentations under heavy furniture. |
Flexibility | Does not flex much, providing a solid, stable surface. | More forgiving and follows minor subfloor imperfections. |
Ideal Use Case | High-traffic homes, commercial spaces, areas prone to heavy impacts. | Budget-friendly home renovations, low-traffic residential areas. |
Moisture & Heat Resistance | Excellent resistance to moisture and climate changes, reducing warping. | Water-resistant, but may expand or contract more under extreme temperatures. |
Cost Considerations | Typically more expensive due to its rigid core and durability. | Wide range of price points, with budget-friendly options available. |
Real-Life Example | Best for kitchens, cafes, and busy households with kids or pets. | Suitable for quiet homes with moderate foot traffic. |
So, while both SPC and regular vinyl share many benefits (like water resistance and easy cleaning), that stone-based core is SPC’s real superpower.
2. Which Core Components Make SPC and Vinyl Flooring Unique?
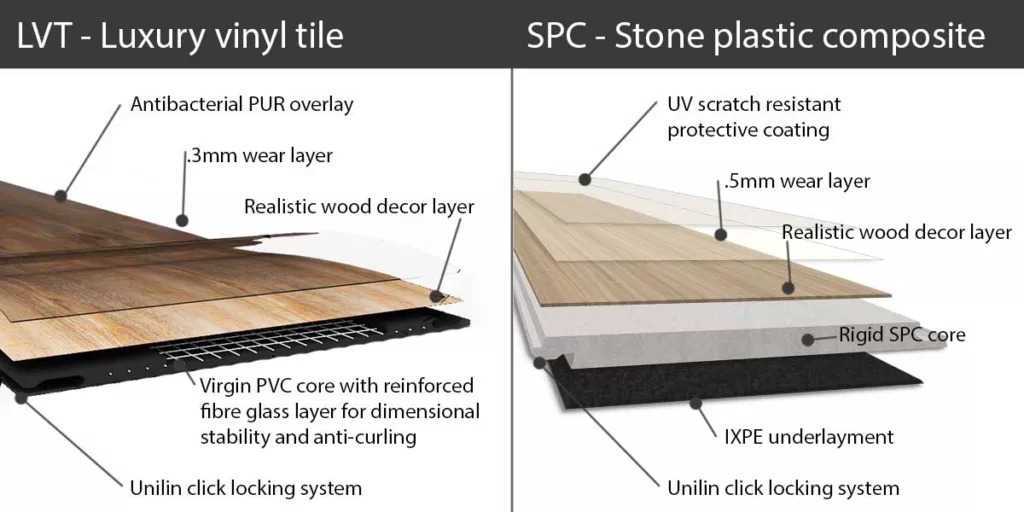
SPC’s rigid core includes limestone powder, adding strength and stability. Vinyl flooring typically has a plasticized PVC core, making it more flexible but slightly less resistant to dents and buckling.
The Core of the Matter
When you hear “core,” think of it like the skeleton of your floor—a hidden framework that greatly affects how well it can handle everything from heavy furniture to changes in room temperature.
2.1 SPC’s Rigid Stone Core
- Limestone (Calcium Carbonate): Makes up a significant portion of the plank’s core. This mineral component drastically reduces the plank’s tendency to expand or contract.
- PVC and Stabilizers: Mixed with the stone to add flexibility and ensure the floor doesn’t snap under pressure.
- Result: A floor that can handle heavier loads, abrupt temperature swings, and minor subfloor imperfections without deforming.
2.2 Vinyl’s More Flexible Makeup
- Pure PVC Layers: Vinyl floors feature layers of PVC, possibly with fiberglass mesh or foam backing, that achieve a balanced mix of durability and comfort.
- Plasticizers for Flex: Used to keep vinyl from becoming too rigid. This can be great if you like a little bounce when you walk.
- Trade-Off: Vinyl’s extra give can mean it’s more prone to dents or contouring to an uneven subfloor.
2.3 Quick Reference Table
Below is a copy-friendly table summarizing the key differences in core composition:
Core Aspect | SPC Flooring | Standard Vinyl Flooring |
---|---|---|
Main Component | Limestone (stone powder) + PVC | Primarily PVC |
Rigidity Level | High (rigid) | Moderate to flexible |
Dimensional Stability | Excellent (minimal expansion) | Good, but can expand/contract in extremes |
Typical Thickness Range | 3.5mm – 7mm+ | 2mm – 6mm+ |
Impact on Comfort | Firmer underfoot | More cushion or bounce |
Use these details to see at a glance how each floor’s “bones” contribute to its performance in the real world.
3. How Do Durability and Performance Vary Between SPC and Traditional Vinyl?

SPC usually outperforms standard vinyl in resisting dents, warping, and expansion. Vinyl still offers durability but can show wear faster under heavy traffic or harsh conditions.
Durability in Everyday Life
When you’re shopping for floors, “durability” might sound abstract. But in practical terms, durability can mean:
- Fewer dents from pet claws or heavy furniture
- Less warping or separating at the seams over time
- Minimal damage when kids spill drinks (or crayons) everywhere
Let’s look at how SPC and standard vinyl compare from multiple angles.
3.1 Resistance to Impact and Scratches
- SPC Flooring:
- Rigid core better resists impacts.
- Excellent for commercial spaces or busy households.
- Thicker wear layers (e.g., 12–20 mil) help ward off scuffs.
- Vinyl Flooring:
- Holds up well but may dent if something heavy sits on it for long periods.
- Scratch resistance varies by brand and wear layer thickness.
3.2 Handling Moisture and Spills
- Both Are Water-Resistant: Vinyl floors (including SPC) are known for their water-resistant or even waterproof claims.
- SPC’s Edge: That rigid core also means less chance of water seeping in and causing the plank to swell or bubble. Still, you should mop up spills quickly.
3.3 Temperature and Climate Challenges
- Expansion/Contraction Concerns:
- Standard vinyl can expand in high heat or contract in cold.
- SPC’s stone core is more stable in these extremes, a boon in climates with big seasonal shifts.
- Sunlight Exposure: Prolonged direct sun may fade the surface of either floor. Using blinds or UV-protective window films can help.
3.4 Real-World Data on Wear Layers
Below is a helpful table that shows typical wear layer thicknesses, their general durability, and suggested usage:
Wear Layer (mil) | Durability Level | Common Usage | Suitable Flooring Type |
---|---|---|---|
6–8 mil | Basic | Low-traffic residential (guest rooms) | Standard Vinyl |
10–12 mil | Moderate | Average household traffic | SPC or Higher-End Vinyl |
20 mil | High | Busy families, light commercial | SPC or Premium Vinyl Planks |
28+ mil | Very High | Heavy commercial (restaurants, retail) | SPC (often commercial-grade) |
The thicker the wear layer, the more a floor can handle daily abuse without losing its good looks.
4. Is SPC More Expensive Than Vinyl?
Typically, yes. SPC flooring costs slightly more because of its stone-based core and high durability, but exact pricing depends on brand, thickness, and wear layer.
Dive Deeper: Crunching the Numbers
Cost considerations can make or break a flooring decision. Let’s explore where SPC and standard vinyl stand on price points.
4.1 Why SPC Often Costs More
- Materials and Manufacturing: The limestone in SPC and the more complex production process push manufacturing costs up.
- Brand Name & Quality: Premium brands that offer thicker wear layers, advanced coatings, and solid warranties tend to charge more.
4.2 Typical Cost Ranges
Here’s a that gives a ballpark sense of costs per square foot in U.S. dollars:
Flooring Type | Approx. Cost (USD/sq. ft.) | Lifespan Estimate | Typical Application |
---|---|---|---|
Basic Vinyl (Sheet or LVT) | $1.00 – $2.50 | 5–10 years | Low-traffic areas, budget projects |
Mid-Range Vinyl (LVP/LVT) | $2.50 – $4.50 | 10–15 years | Residential, moderate traffic |
SPC Flooring (Residential) | $3.50 – $6.00 | 15–25 years | High-traffic homes, variable climates |
SPC Flooring (Commercial) | $5.00 – $7.50+ | 20–30+ years (with care) | Busy retail, offices, industrial |
Note: Prices can vary based on region, retailer, and brand promotions.
4.3 Balancing Upfront vs. Long-Term Costs
- Initial Outlay vs. Durability: SPC can demand a higher initial investment, but its longevity can offset the difference—especially in commercial settings where downtime for repairs is costly.
- Maintenance Savings: A sturdier floor might reduce how often you replace damaged planks or pay for repairs.
If your budget is really tight, a solid mid-range vinyl floor with a decent wear layer might serve you well. However, if you want a “buy once, cry once” scenario, SPC’s durability might make it worth the extra cost.
5. What Is Better, SPC or Vinyl Flooring?
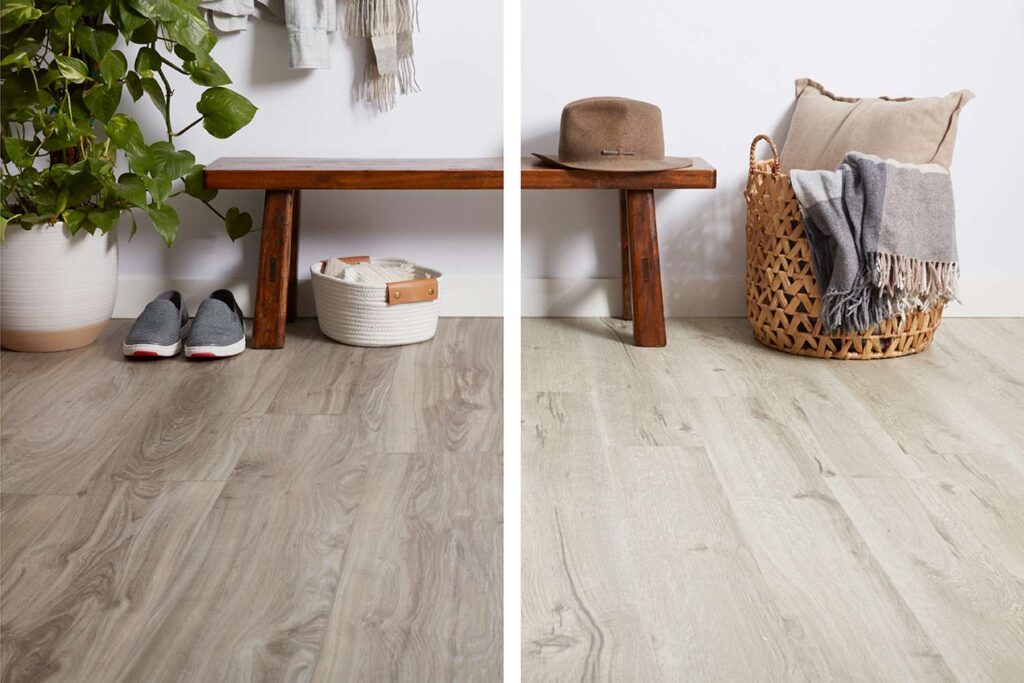
It depends. SPC flooring excels where strength, stability, and long-term resilience are top priorities. Standard vinyl works well in areas with lighter traffic, smaller budgets, or where a softer underfoot feel is preferred.
Weighing the “Best” Option for You
“Better” is subjective, and the right choice depends on your unique scenario.
5.1 Heavy vs. Light Foot Traffic
- High-Traffic Spaces: SPC stands up to scratches, dents, and repeated impact. Ideal for living rooms where you host frequent parties or a bustling commercial shop.
- Low-Traffic Spaces: Bedrooms or guest rooms might not need the rigidity (and cost) of SPC. A good vinyl plank could be enough.
5.2 Room Conditions and Environment
- Temperature Swings: If you live somewhere that’s scorching in summer but frigid in winter, SPC’s minimal expansion is reassuring.
- Humidity and Moisture: Both are water-resistant, but again, SPC handles moisture infiltration with fewer issues if installed properly.
5.3 Budget Constraints
- Initial Purchase: Standard vinyl is typically cheaper, letting you allocate funds to other home improvements.
- Future Replacements: If you expect your floors to endure a lot of wear, investing in SPC might save you from replacing them prematurely.
5.4 Personal Comfort and Style
- Underfoot Feel: Vinyl can be softer, especially if it has a cushioned underlayment. SPC can feel sturdier, but some say it’s less “giving.”
- Aesthetic Versatility: Both come in myriad designs—wood grain, stone patterns, even bold geometric prints.
Factor | SPC Flooring (Stone Plastic Composite) | Standard Vinyl Flooring |
---|---|---|
Foot Traffic | Ideal for high-traffic areas, commercial spaces, and active households. | Best for low to moderate foot traffic areas like bedrooms or guest rooms. |
Room Conditions | Minimal expansion/contraction in extreme temperatures, great for variable climates. | More susceptible to temperature swings and expansion/contraction. |
Moisture Resistance | Highly resistant to water infiltration, making it ideal for kitchens and bathrooms. | Also water-resistant, but lower-quality options may allow seepage over time. |
Budget Considerations | Generally more expensive upfront but offers long-term durability. | More budget-friendly initially, but may need replacement sooner in high-wear areas. |
Underfoot Comfort | Feels firmer and sturdier, less cushioned. | Softer feel, especially with cushioned underlayment. |
Aesthetic Options | Available in various wood, stone, and tile designs. | Wide range of styles, including bold geometric prints and classic wood looks. |
In a nutshell, the “best” floor is the one that aligns with your traffic level, climate, comfort preference, and finances.
6. Are Installation Methods the Same for SPC and Vinyl Flooring?
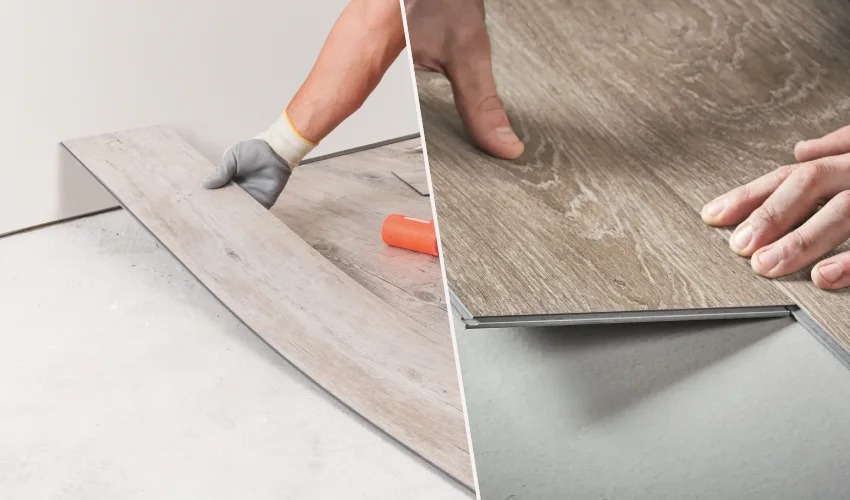
Yes—both SPC and vinyl often use floating click-lock or glue-down methods. However, SPC’s rigid core might require more attention to subfloor leveling, as it’s less forgiving than flexible vinyl.
Laying Down the Basics
Whether you choose SPC or a vinyl plank, the installation technique can make or break your flooring’s longevity and appearance.
6.1 Floating Click-Lock
- How It Works: Planks click together around the edges and “float” over the subfloor. No glue is required.
- Pros:
- Faster installation, especially for DIYers.
- Easier to replace individual planks if they get damaged.
- Cons:
- Subfloor imperfections could cause slight gaps or squeaks.
- Must allow proper expansion gaps around the room perimeter.
6.2 Glue-Down Approach
- How It Works: Adhesive is spread over the subfloor, and each plank is pressed into place.
- Pros:
- Very secure—great for commercial settings or high-traffic areas.
- Typically less movement or shifting over time.
- Cons:
- More labor-intensive.
- Harder to replace single damaged planks.
6.3 Subfloor Prep Essentials
- SPC Flooring:
- Rigid, so it can bridge over minor dips, but large bumps or valleys must still be leveled.
- If the subfloor is seriously uneven, you risk stress on the locking joints.
- Regular Vinyl:
- Thinner, flexible vinyl can sometimes mirror subfloor imperfections (like lumps or cracks).
- An unprepared subfloor may lead to visible ridges or “telegraphing.”
6.4 DIY vs. Professional
- DIY Suitability:
- Many homeowners have successfully installed both SPC and vinyl plank. Floating floors are generally more forgiving for novices.
- Professional Touch:
- A pro will identify subfloor issues you might miss, ensure correct expansion gaps, and often provide a warranty on labor.
Factor | SPC Flooring (Stone Plastic Composite) | Standard Vinyl Flooring |
---|---|---|
Floating Click-Lock | Planks snap together without glue, creating a “floating” floor. | Uses the same click-lock system for easy installation. |
Click-Lock Pros | Fast DIY installation, easy to replace damaged planks. | Quick to install, forgiving for DIY projects. |
Click-Lock Cons | Requires a level subfloor to prevent gaps or squeaks. | Subfloor imperfections may be more visible. |
Glue-Down Method | Adhesive is applied to the subfloor for a secure hold. | Same method; ensures long-term stability in high-traffic areas. |
Glue-Down Pros | Very stable, ideal for commercial or high-traffic spaces. | Less movement or shifting over time. |
Glue-Down Cons | More labor-intensive, harder to replace single planks. | Requires time for adhesive to cure properly. |
Subfloor Preparation | Bridges small dips but requires leveling for major imperfections. | More flexible but may show subfloor imperfections (“telegraphing”). |
DIY vs. Professional | DIY-friendly but benefits from professional leveling. | DIY-friendly, though pros can ensure proper subfloor prep and longevity. |
Overall, the installation method for SPC vs. vinyl isn’t drastically different. Focus on thorough subfloor prep and follow the manufacturer’s instructions for best results.
7. Do Maintenance and Care Requirements Differ for SPC Versus Vinyl?
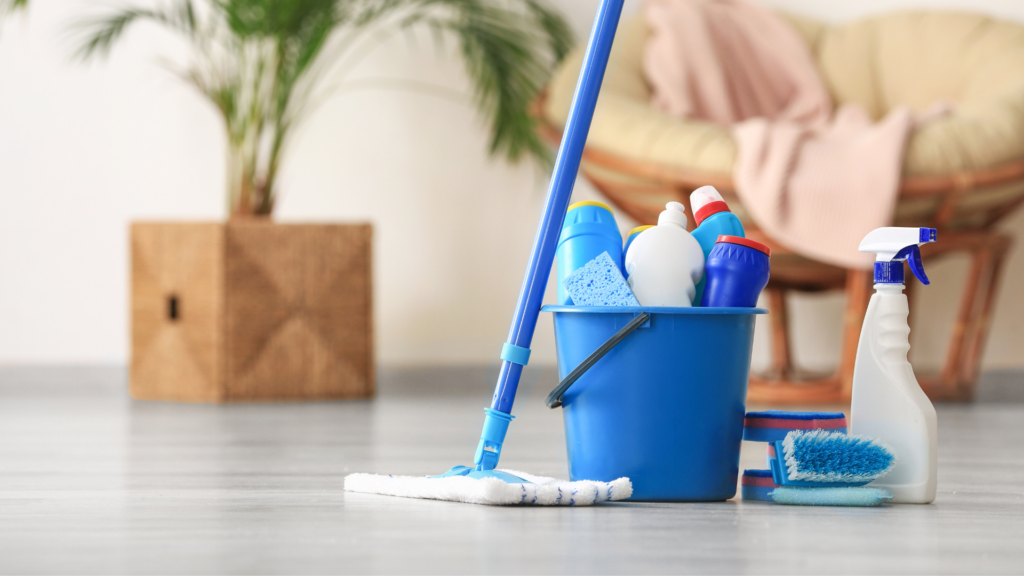
They’re similar. Both need regular sweeping or vacuuming, prompt spill cleanups, and gentle cleaners. SPC’s rigid core offers a slight edge in resisting water damage, but upkeep is basically the same.
Maintaining That Like-New Look
Long after you’ve installed your floor, day-to-day maintenance is what keeps it looking showroom-ready.
7.1 Daily or Weekly Cleaning
- Sweeping and Vacuuming: Gritty dirt can act like sandpaper, scuffing the top wear layer. A quick sweep or vacuum can work wonders.
- Damp Mopping: Use a mild, pH-neutral cleaner formulated for vinyl floors. Avoid excess water to prevent it from seeping into the seams (though SPC is more tolerant if water lingers briefly).
7.2 Spills and Stains
- Immediate Cleanup: Even though both types resist water, letting liquids pool can cause problems around edges or under planks if left too long.
- No Harsh Chemicals: Bleach or abrasive cleaners may dull the surface or damage the wear layer over time.
7.3 Furniture and Foot Traffic
- Furniture Pads: Attach felt pads or floor protectors under heavy furniture legs to reduce denting and scratching—especially for standard vinyl.
- Rugs and Mats: Place doormats at entrances to trap dirt. For high-traffic areas, area rugs can reduce direct wear on the floor’s surface.
7.4 Periodic Deep Cleaning
- Every Few Months: Consider a deeper cleaning session with a specialized vinyl floor cleaner if everyday dirt accumulates.
- Avoid Waxing (Unless Specified): Modern vinyl (including SPC) usually doesn’t require waxing. Check manufacturer guidelines for finishing products or polishes.
When it comes to routine upkeep, SPC and standard vinyl are equally low maintenance. A simple cleaning regimen can help both types keep their luster for many years.
8. When Should You Choose SPC Flooring Over Other Vinyl Options?
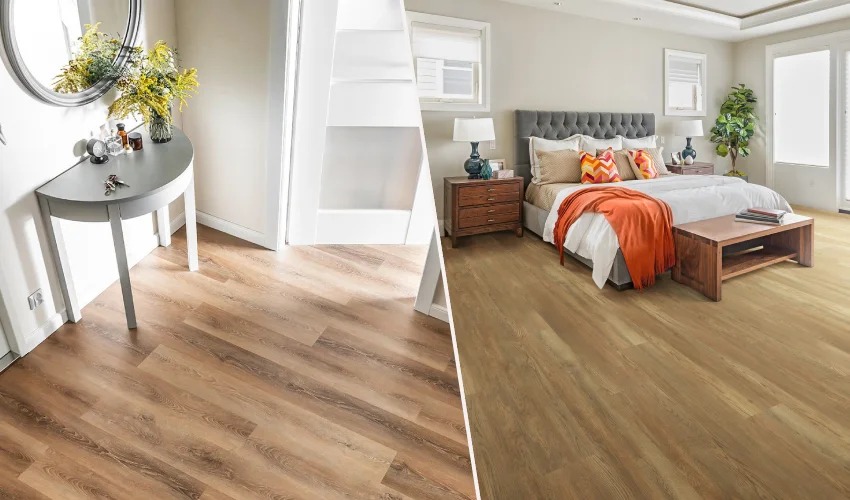
Opt for SPC if you need a tough, stable floor in high-traffic, temperature-variable, or moisture-prone areas. It’s especially good for commercial spaces or busy households expecting heavy wear and tear.
Deciding Factors for Your Specific Needs
At this point, you might be leaning one way or the other, but let’s highlight a few more real-world scenarios where SPC truly shines.
8.1 Commercial or High-Use Residential
- Retail Stores, Restaurants, Offices: SPC’s stone core resists dents from rolling carts, high heels, and frequent foot traffic. Over time, this can mean fewer replacements and less disruption to business.
- Busy Households: Got kids, pets, or large family gatherings? SPC’s rigidity ensures those random dropped items or muddy paw prints won’t do much damage.
8.2 Extreme Temperature Swings or Humidity
- Seasonal Homes (Cabins, Vacation Rentals): If the property isn’t climate-controlled year-round, SPC’s minimal expansion/contraction helps avoid warped boards when no one’s around.
- Coastal or Tropical Climates: High humidity can accelerate damage in regular vinyl floors, but SPC’s robust makeup handles moisture with fewer issues.
8.3 Subfloor Challenges
- Slightly Uneven Subfloor: SPC planks can mask minor subfloor imperfections better than thin vinyl, though major lumps still need fixing.
- Floating Installations: If you prefer a floating system with minimal floor prep, SPC’s rigidity often provides a more secure “locked” feel.
8.4 Long-Term Savings and Aesthetics
- Reduced Need for Early Replacement: Spending a bit more on SPC up front could save you from replacements or extensive repairs within a decade.
- Realistic Textures and Finishes: Many SPC lines offer deeply embossed wood or stone textures, which can elevate the visual appeal of your space.
Conclusion: Ready to Invest in the Right Flooring? Contact Kinwin
Choosing the right floor isn’t about picking the “best” material in a vacuum—it’s about finding the perfect match for your home or business. SPC flooring offers a formidable mix of durability, stability, and impressive longevity, making it a top pick if you expect heavy traffic, shifting temperatures, or just want serious peace of mind. Standard vinyl, meanwhile, remains a fantastic option for many folks who want a comfortable, stylish floor without stretching their budget too far.
Either way, a few fundamentals remain constant:
- Invest in a quality product with an adequate wear layer.
- Ensure proper installation (subfloor prep can’t be ignored!).
- Keep up with simple maintenance—sweep, mop, and protect it from potential damage.
Still not sure which way to go? We at Kinwin can help you cut through the guesswork and arrive at a flooring solution that suits your unique needs—be it SPC, traditional vinyl, or another top-tier option. Ready to level up your floors and get a custom quote? Reach out today and let’s explore how we can bring both style and durability to your space, one plank at a time.