Laying down vinyl plank flooring is like giving your space a glow-up—think sleek wood vibes without the hefty price tag. But mess up the install, and you’re stuck with wobbly planks, ugly gaps, or a floor that fails in a year. Avoiding rookie mistakes is key to a floor that looks fire and lasts forever. So, what are the big no-nos when installing vinyl plank?
Common vinyl plank flooring installation mistakes include poor subfloor prep, using wrong tools, misaligned planks, improper adhesive, ignoring humidity, and skipping curing or cleanup.
Imagine you’re jazzed to install your new vinyl plank floor, picturing a cozy, hardwood-look living room. Halfway through, you spot crooked seams and wobbly spots—total buzzkill! Don’t let your floor dreams flop. Hang with me, and I’ll spill the tea on the most common installation mistakes and how to dodge them like a flooring pro.
Why Do Installation Mistakes Matter for Vinyl Plank Flooring?
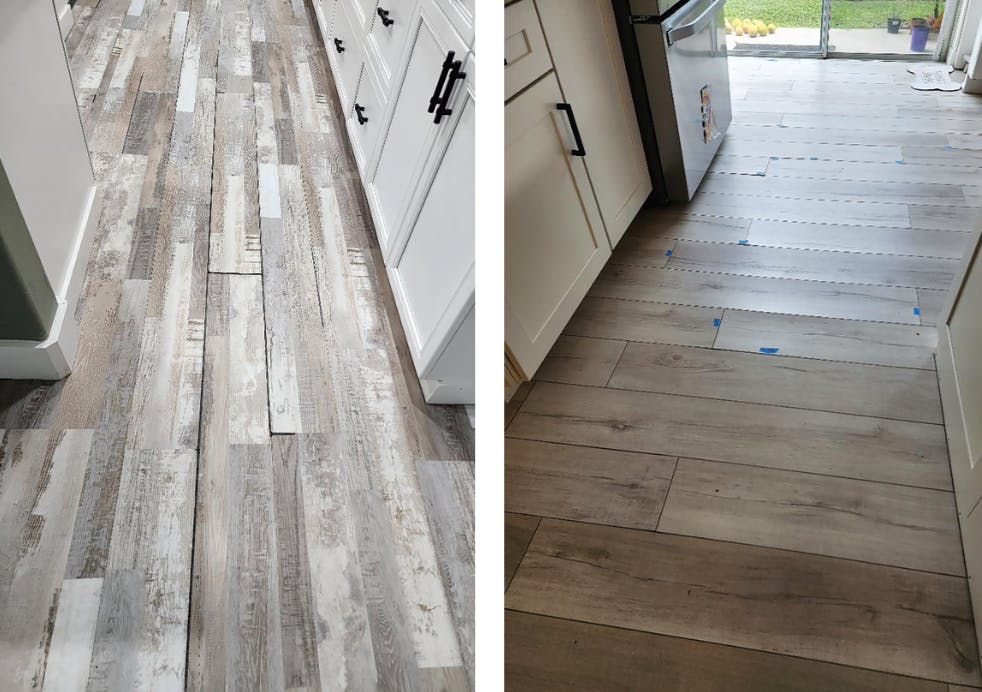
Installation mistakes lead to uneven floors, gaps, or early wear, costing hundreds to fix.
Why Screwing Up Your Install Is a Nightmare
Kills Your Floor’s Lifespan
Vinyl plank can rock your space for 10-20 years, but slip-ups like a bumpy subfloor or bad adhesive can cut that short, causing cracks or lifting. A 2025 flooring study says 60% of vinyl floor fails come from shoddy installs. Critically, ask: are you setting your floor up for a long, happy life or an early grave?
Tanks the Vibe
Nothing screams “oops” like gaps, crooked planks, or bubbles in your floor. It’s like wearing mismatched shoes—it just looks wrong. A homeowner’s misaligned planks turned their kitchen into a patchwork mess. Reflect: wanna keep your floor looking like it belongs on Instagram?
Hits Your Wallet Hard
Fixing a botched install—think replacing warped planks or hiring a pro—can cost $500-$2,000, depending on the damage. Doing it right the first time saves serious cash. A client avoided a $1,500 redo by nailing their prep. Think: wouldn’t you rather spend that money on a new couch or a vacation?
Stresses You to the Max
A bad install means delays, frustration, and maybe even starting over. A DIYer nearly cried when their rushed install left a wavy floor that needed fixing. Ask: want a chill, smooth install or a total headache?
Makes Your Space Feel Cheap
A sloppy floor drags down your whole room’s vibe, making it look like a budget job, even if the planks are top-notch. A retailer’s uneven floor had customers noticing the flaws instead of the decor. Think: can a perfect install make your space feel like a million bucks?
Problema | Perché è un male | Esempio del mondo reale | Who Gets Burned |
---|---|---|---|
Shortened Lifespan | Cracks, lifting cut life short | Floor failed in 2 years | Proprietari di case, aziende |
Ruined Aesthetic | Gaps, uneven seams look sloppy | Patchy kitchen floor | Amanti del design |
High Repair Costs | Expensive fixes or full redo | $1,500 redo avoided | Attenti al budget |
Stress and Delays | Frustration, rework time | DIYer’s wavy floor struggle | DIYers, renovators |
Cheap-Looking Space | Drags down room’s vibe | Retail floor distracted customers | Ospiti, rivenditori |
What Are the Most Common Subfloor Preparation Mistakes?
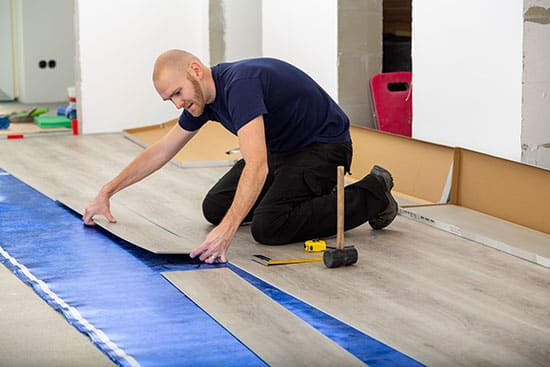
Skipping leveling, cleaning, or moisture testing causes uneven or lifting vinyl plank floors.
Subfloor Prep Fails You Can’t Afford
Not Leveling the Subfloor
Your subfloor needs to be flat—within 3/16” over 10 feet—or planks will wobble, crack, or pop up. A DIYer’s unlevel concrete slab made their living room floor feel like a funhouse. Critically, ask: is your subfloor smooth enough to keep your planks steady?
Forgetting to Clean
Dust, grease, or tiny debris stops adhesive or click-lock from gripping, leading to loose planks. A client’s greasy subfloor caused their glue-down vinyl to peel in weeks. Reflect: are you scrubbing and sweeping your subfloor before laying down planks?
Ignoring Moisture Problems
Damp subfloors spell disaster—think warped planks or mold growth. A 2025 report says 30% of vinyl issues come from unchecked moisture. A homeowner used a moisture meter ($20) in their basement to dodge a moldy mess. Think: have you tested your subfloor to keep it dry?
Leaving Old Flooring Behind
Keeping old carpet, cracked tiles, or uneven wood under vinyl creates a shaky base, causing planks to shift or crack. A renter’s carpet underlay made their click-lock floor wobble. Ask: are you ripping out old flooring to start fresh?
Skipping Subfloor Repairs
Cracks, holes, or loose boards in the subfloor weaken your install, leading to squeaks or dips. A client patched their plywood subfloor to avoid a creaky floor. Think: are you fixing subfloor flaws for a rock-solid base?
Errore | What Goes Wrong | How to Fix It | Cost to Fix | Strumento necessario |
---|---|---|---|---|
Not Leveling | Wobbly, cracked planks | Use leveling compound | $100-500 | Level, compound ($20) |
Skipping Cleaning | Poor adhesion, lifting | Sweep, mop with cleaner | $0-20 | Broom, cleaner ($5) |
Ignoring Moisture | Warping, mold growth | Test moisture, add barrier | $50-200 | Moisture meter ($20) |
Leaving Old Flooring | Unstable base, shifting | Remove old materials | $100-1,000 | Pry bar ($10) |
Skipping Repairs | Squeaks, dips | Patch cracks, secure boards | $50-300 | Patching kit ($15) |
How Do Incorrect Tools and Materials Cause Installation Problems?
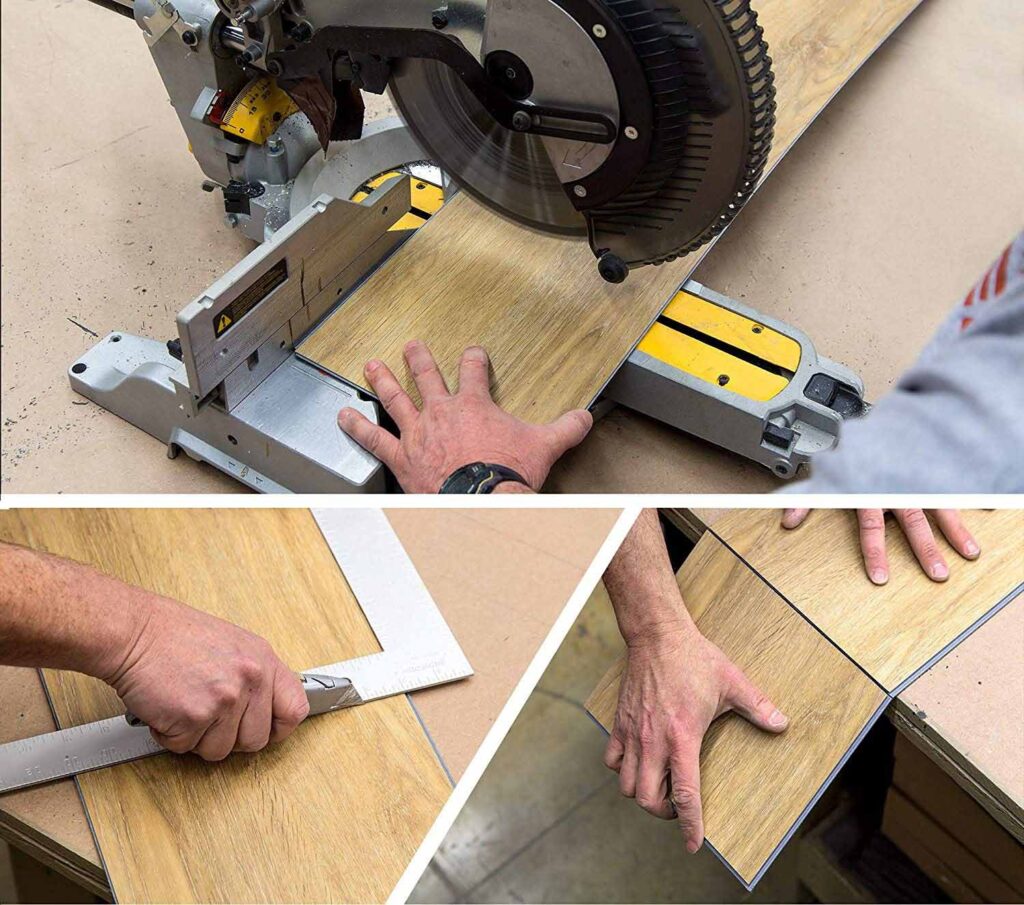
Wrong adhesives, dull blades, or no spacers cause weak bonds or uneven vinyl plank floors.
Tool and Material Blunders to Skip
Using the Wrong Adhesive
For glue-down vinyl, non-vinyl adhesive ($20/gallon) won’t hold, causing planks to lift or slide. A client’s generic glue failed in a high-traffic shop. Critically, ask: are you grabbing vinyl-specific adhesive for your glue-down install?
Dull or Wrong Cutting Tools
A dull utility knife ($5) or cheap saw mangles plank edges, leaving gaps or rough seams. A DIYer’s dull blade made their floor look sloppy. Reflect: do you have sharp, precise tools for clean, pro-level cuts?
Forgetting Spacers for Click-Lock
Skipping 1/4” spacers ($3) in click-lock installs traps planks, causing buckling when they expand. A homeowner’s tight install warped in humid summer heat. Think: are you leaving expansion gaps to let your floor breathe?
Cheap or Wrong Underlayment
Low-quality underlayment ($0.20/sq. ft.) or one meant for laminate makes your floor noisy or unstable. A client’s thin underlay caused a hollow sound underfoot. Ask: is your underlayment vinyl-approved and thick enough?
No Tapping Block for Click-Lock
Forcing click-lock planks without a tapping block ($10) damages edges, ruining the lock. A DIYer’s hammered planks left gaps. Think: are you using a tapping block to gently lock planks?
Errore | Problem | Soluzione | Cost to Fix | Tool Cost |
---|---|---|---|---|
Wrong Adhesive | Weak bond, lifting planks | Use vinyl-safe adhesive | $100-500 | $20/gallon |
Dull Cutting Tools | Jagged edges, gaps | Sharp utility knife, saw | $50-200 | $5-50 |
Nessun distanziatore | Buckling, no expansion space | Use 1/4” spacers | $100-300 | $3 |
Poor Underlayment | Noise, instability | Vinyl-specific underlay | $100-400 | $0.50/sq. ft. |
No Tapping Block | Damaged click-lock edges | Use tapping block, mallet | $50-200 | $10 |
What Happens When You Misjudge Plank Placement and Patterns?
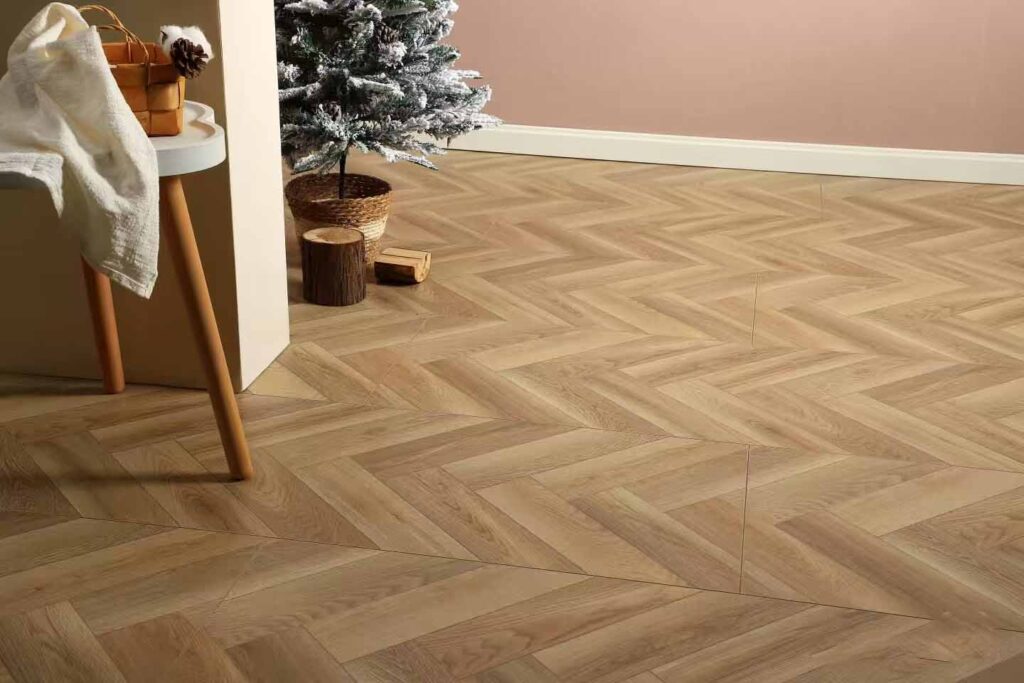
Misaligned planks, unstaggered seams, or no pattern plan cause gaps or uneven vinyl floors.
Placement and Pattern Whoopsies to Avoid
Misaligning Planks
Crooked planks create uneven seams or gaps that scream amateur. A DIYer’s rushed install left wavy lines across their dining room floor. Critically, ask: are you using a chalk line or straightedge to keep planks perfectly aligned?
Not Staggering Seams
Lining up seams in rows looks fake and weakens the floor’s structure. A client’s unstaggered planks shifted under heavy furniture. Reflect: are you randomizing seam placement for a natural, sturdy look?
Skipping Pattern Planning
Not sketching out complex patterns like herringbone or diagonal leads to uneven cuts or running out of planks. A homeowner’s unplanned chevron pattern wasted $200 in materials. Think: have you mapped out your floor’s design to avoid shortages?
Forgetting Expansion Gaps
No 1/4” gap around walls or fixtures traps planks, causing buckling in heat or humidity. A renter’s gapless install popped up in July. Ask: are you leaving expansion space to let your floor flex?
Ignoring Plank Direction
Laying planks against the room’s light or flow makes seams stand out awkwardly. A client flipped their planks to follow sunlight for a seamless look. Think: are you laying planks to match your room’s vibe?
Errore | Problema | Fissare | Impatto | Strumento necessario |
---|---|---|---|---|
Misaligned Planks | Crooked seams, gaps | Use chalk line, straightedge | Sloppy look | Chalk line ($5) |
Unstaggered Seams | Weak structure, unnatural look | Randomize seams | Shifting planks | Nessuno |
No Pattern Plan | Wasted planks, uneven cuts | Sketch pattern first | Costo aggiuntivo | Graph paper ($3) |
No Expansion Gaps | Buckling, popping | Leave 1/4” gaps | Warped floor | Spacers ($3) |
Wrong Plank Direction | Awkward seams, bad flow | Follow light or room flow | Unbalanced aesthetic | Nessuno |
Are You Making Mistakes with Adhesive or Click-Lock Systems?
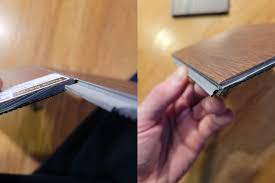
Over-applying adhesive or forcing click-lock planks causes bubbles, weak bonds, or damaged vinyl floors.
Adhesive and Click-Lock Fumbles
Over- or Under-Applying Adhesive
Too much glue ($20/gallon) creates bubbles under planks; too little lets them lift. A client’s heavy-handed glue spread caused lumps in their shop floor. Critically, ask: are you using a notched trowel to spread adhesive just right?
Forcing Click-Lock Planks
Jamming click-lock planks together damages the locking edges, leaving gaps or weak connections. A DIYer’s forced planks wouldn’t lock properly, creating seams. Reflect: are you gently tapping click-lock pieces with a mallet?
Using Old or Non-Vinyl Glue
Expired or generic glue fails to hold, causing planks to peel or slide. A homeowner’s outdated glue ruined their kitchen install. Think: are you checking your glue’s type and expiration date?
Not Cleaning Glue Spills Fast
Glue drips left on planks harden into sticky spots or discolor the surface. A client wiped spills with a damp cloth to keep their floor pristine. Ask: are you cleaning adhesive messes ASAP?
Ignoring Click-Lock Angle
Click-lock planks need a 15-30° angle to snap in smoothly. Wrong angles break the lock. A client mastered the angle for a tight fit. Think: are you locking planks at the right angle?
Errore | Problem | Soluzione | Cost to Fix | Strumento necessario |
---|---|---|---|---|
Wrong Adhesive Amount | Bubbles, lifting | Use notched trowel evenly | $100-500 | Trowel ($10) |
Forcing Click-Lock | Damaged edges, gaps | Tap gently with mallet, block | $50-200 | Mallet, block ($15) |
Old/Wrong Glue | Peeling, sliding planks | Use fresh, vinyl-safe glue | $200-1,000 | Vinyl glue ($20) |
Uncleaned Spills | Sticky spots, discoloration | Wipe spills with damp cloth | $0-50 | Cloth ($2) |
Wrong Click-Lock Angle | Broken locks, loose planks | Use 15-30° angle | $50-200 | Nessuno |
How Does Ignoring Environmental Factors Affect Installation?
Wrong temperatures, high humidity, or no acclimation cause vinyl plank warping or expansion issues.
Environmental Goofs That Wreck Floors
Installing in Wrong Temperatures
Vinyl needs 60-80°F during install—too cold makes planks brittle, too hot makes them mushy. A client’s freezing garage install cracked their planks. Critically, ask: are you checking the room’s temp to keep planks happy?
High Humidity Havoc
Humidity over 60% makes planks swell or stops adhesive from setting, leading to warping. A beach house install buckled in humid conditions. Reflect: have you got a dehumidifier or hygrometer ($15) to control moisture?
Skipping Acclimation Time
Planks need 48 hours in the install room to adjust to its temp and humidity. A rushed install without acclimation caused planks to shrink. Think: are you letting your planks chill before laying them?
Poor Ventilation for Glue-Down
Glue-down installs need airflow to cure adhesive and clear fumes, or the bond weakens. A client’s stuffy room led to a loose floor. Ask: are you opening windows or using fans for glue-down installs?
Ignoring Seasonal Changes
Installing in extreme seasons (like humid summers) without climate control causes expansion issues later. A homeowner waited for spring for a stable install. Think: are you timing your install for balanced conditions?
Errore | Problema | Fissare | Impatto | Strumento necessario |
---|---|---|---|---|
Wrong Temperature | Brittle or mushy planks | Keep 60-80°F | Cracked planks | Thermometer ($10) |
High Humidity | Swelling, adhesive failure | Use dehumidifier, hygrometer | Warped floor | Hygrometer ($15) |
No Acclimation | Shrinking, buckling | Acclimate 48 hours | Uneven surface | Nessuno |
Poor Ventilation | Weak adhesive, trapped fumes | Open windows, use fans | Loose planks | Fan ($20) |
Wrong Season | Expansion in extreme conditions | Install in mild seasons | Future buckling | Nessuno |
What Are the Risks of Skipping Post-Installation Steps?
Skipping curing, cleanup, or furniture pads risks loose, scratched, or unstable vinyl plank floors.
Dive Deeper: Post-Install Mistakes That Bite
Rushing Cure Time
Glue-down floors need 24-48 hours to set; walking or moving furniture too soon weakens the bond. A client’s early couch placement shifted their planks. Critically, ask: are you giving adhesive enough time to lock in tight?
Forgetting Cleanup
Glue drips, dust, or debris left on the floor create sticky spots or scratches. A homeowner’s quick sweep and wipe kept their floor sparkling. Reflect: are you cleaning up post-install to protect that fresh look?
No Furniture Pads
Heavy furniture without felt pads ($5 for 20) scratches or dents your new floor. A client’s dining table left marks without pads. Think: are you slapping pads on furniture to save your planks?
Skipping Initial Maintenance
Not sweeping daily or cleaning spills fast leads to early wear or stains. A retailer’s daily sweep kept their floor showroom-ready. Ask: are you kicking off maintenance to keep your floor fresh?
Not Inspecting the Install
Missing small gaps or loose planks early can worsen over time. A DIYer caught a loose plank early and saved a bigger fix. Think: are you checking your install for tiny flaws before calling it done?
Errore | Problem | Soluzione | Cost to Fix | Strumento necessario |
---|---|---|---|---|
No Cure Time | Weak adhesive, shifting planks | Wait 24-48 hours | $200-1,000 | Nessuno |
Skipping Cleanup | Sticky spots, scratches | Sweep, wipe glue residue | $0-50 | Broom, cloth ($5) |
No Furniture Pads | Scratches, dents | Use felt pads | $50-200 | Pads ($5) |
Poor Initial Maintenance | Early wear, stains | Sweep daily, clean spills | $100-500 | Broom ($10) |
No Inspection | Missed gaps, loose planks | Check seams, press planks | $50-300 | Flashlight ($5) |
Wrap-Up: Ace Your Vinyl Plank Install with Kinwin
Getting your vinyl plank flooring install right means dodging pitfalls like bad subfloor prep, wrong tools, misaligned planks, or rushing the process. Nail it, and you’ll have a stunning, durable floor that lasts for years. At Kinwin, we’re all about crafting eco-friendly, high-quality vinyl plank flooring that’s tough, gorgeous, and ready for your space. Want a custom floor or expert installation tips? Contact Kinwin today for a quote or to create your dream space. Let’s make your floors a total showstopper!